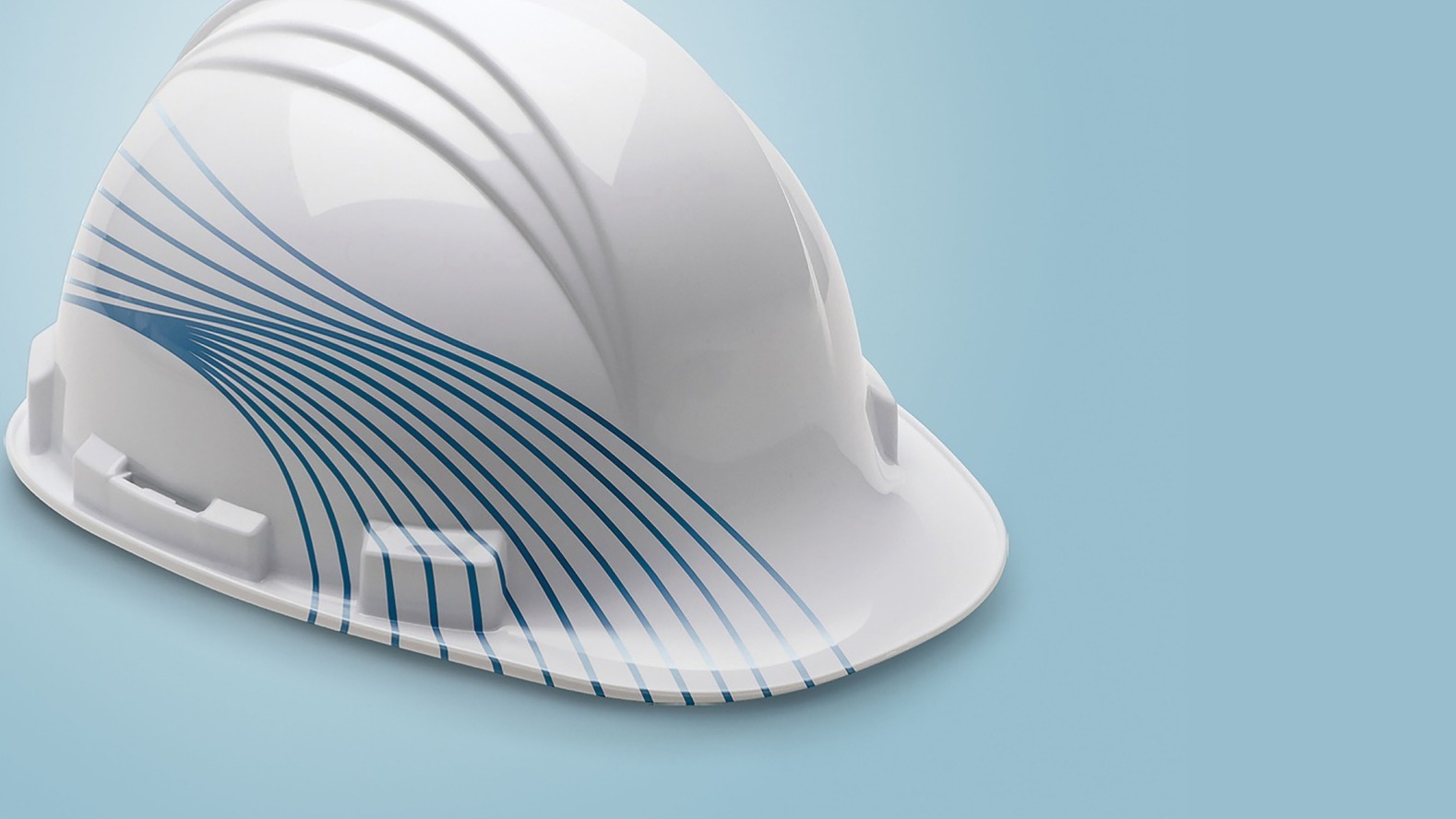
10 Mistakes Contractors Make with Insulation Services
Common Mistakes Contractors Make and Prevention Tips
Introduction
When it comes to insulation services, contractors play a vital role in ensuring the effectiveness and efficiency of the insulation in a building. However, there are common mistakes that contractors can make during the insulation installation process that can compromise the performance and longevity of the insulation.
In this article, we'll talk about the most common mistakes insulation contractors make and tips on how to prevent them.
10 Mistakes Contractors Make with Insulation Services
1. Inadequate Assessment of Insulation Needs
One of the most critical mistakes contractors can make is not conducting a thorough assessment of the insulation needs of a building. Insulation requirements can vary depending on factors such as climate, building design, and energy efficiency goals. Failing to assess these needs properly can lead to the installation of inadequate or excessive insulation, resulting in energy loss or unnecessary costs.
2. Incorrect Insulation Material Selection
Choosing the right insulation material is crucial for optimal performance. Contractors may make the mistake of using the wrong type of insulation material for a particular application. Each insulation material has its unique properties and suitability for specific areas of a building. Selecting the wrong material can lead to reduced insulation effectiveness and potential issues such as moisture buildup or inadequate thermal resistance.
3. Insufficient Air Sealing
Proper air sealing is essential for preventing air leakage and maintaining insulation efficiency. Contractors may neglect the importance of air sealing or fail to execute it effectively. Gaps, cracks, or improperly sealed areas can allow air infiltration, compromising the insulation's ability to control temperature and moisture. Thorough air sealing should be a priority during insulation installation.
4. Incomplete Coverage and Gaps
Ensuring complete coverage and avoiding gaps in insulation is crucial for optimal performance. Contractors may rush the installation process, leading to uneven coverage or leaving gaps in the insulation layer. These gaps can create thermal bridges, allowing heat transfer and reducing the overall insulation effectiveness. Thorough and meticulous installation is necessary to achieve uniform insulation coverage.
5. Improper Installation Techniques
Improper installation techniques can significantly impact the insulation's performance. Contractors may overlook important installation guidelines, such as proper placement, fastening, or handling of insulation materials. These oversights can result in compressed insulation, voids, or compromised integrity, reducing the insulation's ability to provide the desired thermal resistance and energy efficiency.
6. Neglecting Vapor Barrier Installation
Vapor barriers are essential components of insulation systems, especially in moisture-prone areas. Contractors may overlook the installation of vapor barriers or fail to install them correctly. Without a properly installed vapor barrier, moisture can penetrate the insulation and lead to mold growth, reduced insulation effectiveness, and potential damage to the building structure. Contractors should ensure the appropriate installation of vapor barriers where required.
7. Ignoring Safety Precautions
Contractors should prioritize safety during insulation services, both for themselves and the building occupants. Neglecting safety precautions can result in accidents, health risks, or damage to the property. Contractors should use personal protective equipment (PPE), follow safety guidelines, and adhere to local building codes and regulations to ensure a safe working environment.
8. Lack of Quality Control Measures
A lack of quality control measures can contribute to subpar insulation services. Contractors may not implement proper quality control processes to monitor the installation, verify compliance with industry standards, or identify potential issues. Implementing robust quality control measures, including inspections and testing, is essential to ensure the insulation meets the desired performance standards.
9. Failure to Educate Clients on Maintenance
Contractors often overlook the importance of educating clients on insulation maintenance. Insulation requires regular upkeep and periodic inspections to maintain its performance. Contractors should provide clients with guidelines and recommendations for maintaining the insulation, such as proper cleaning, monitoring for signs of damage or moisture, and scheduling professional inspections.
10. Lack of Proper Documentation
Proper documentation is vital for insulation services, including project specifications, material information, and warranties. Contractors may neglect thorough documentation, making it challenging for clients to access essential information in the future. Maintaining comprehensive records and providing clients with necessary documentation ensures transparency, facilitates future maintenance or upgrades, and enhances the overall customer experience.
Tips to Prevent These Mistakes
Thorough Inspections: Conduct comprehensive assessments of the property before recommending insulation solutions. Consider factors such as building design, climate zone, and client requirements.
Proper Material Selection: Choose insulation materials that are suitable for the specific application and climate zone. R-value, durability against moisture, and protection from fire are a few things to think about.
Quality Installation: Ensure that insulation installation is carried out by trained and certified professionals. Follow industry best practices, including proper sealing of air leaks and maintaining proper ventilation.
Safety Measures: Prioritize safety during the installation process. Provide proper personal protective equipment (PPE) to workers, follow safety protocols, and adhere to local building codes and regulations.
Clear Communication: Maintain open and regular communication with clients. Discuss project timelines, expectations, and any potential challenges. Address client concerns promptly and provide updates throughout the insulation project.
Educate Clients: Educate clients about insulation maintenance and best practices. Provide guidelines for cleaning, monitoring, and scheduling professional inspections. Emphasize the importance of regular upkeep to ensure optimal insulation performance.
Thorough Documentation: Maintain comprehensive project documentation, including project specifications, material information, and warranties. Provide clients with copies of relevant documents for future reference.
Continuous Training: Invest in ongoing training and certification programs for insulation professionals. Stay updated on industry trends, new technologies, and energy efficiency considerations.
Energy Efficiency Assessments: Prioritize energy efficiency assessments during insulation projects. Consider factors like building orientation, solar heat gain, and the insulation's thermal resistance. Recommend solutions that align with clients' sustainability goals.
Post-Installation Evaluation: Conduct post-installation evaluations to assess insulation performance. Schedule follow-up inspections, address any issues, and offer ongoing support to clients. Evaluate long-term energy savings and potential warranty claims.
Conclusion
Avoiding these common mistakes can help contractors provide exceptional insulation services and ensure the long-term performance and energy efficiency of the insulation. By conducting thorough assessments, using appropriate materials and techniques, prioritizing safety and quality control, and educating clients, contractors can deliver insulation solutions that meet the highest standards. It is essential for contractors to stay informed, keep up with industry best practices, and continuously improve their insulation services.